Electrical Safety Works
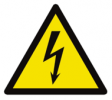
The following electrical safety works shall be carried out:
1. Electrical safety inspection of premises: The inspection is carried out in compliance with Rule 16 (3) of the Fire Risk Reduction Rules, 2007 which requires that every occupier ensures that all electrical equipment and the related attachments are inspected in every period of six months by a competent person and a record of the inspection kept. The following specifics shall be carried out.
- Review of the entire electrical safe work program both for energized and energized work;
- Reviewing written electrical safe operating/work procedures;
- Confirming suitability of personal protective equipment (PPE) issued;
- Inspection of electrical equipment and systems for compliance; and
- Carrying out a root cause analysis of the deficiencies identified
2. Earthing and bonding tests: “Earthing” is a term used to indicate a direct or indirect connection to the planet Earth or to some conducting body that serves in place of the Earth. The connection(s) to Earth can be intentional or unintentional by an assortment of metallic means intended to be employed as a designated grounding electrode. “Bonding” is a method by which all electrically conductive materials and metallic surfaces of equipment and structures, not normally intended to be energized, are effectively interconnected together via a low impedance conductive means and path in order to avoid any appreciable potential difference between any separate points. The bonded interconnections of any specific electrically conductive materials, metallic surfaces of enclosures, electrical equipment, pipes, tubes, or structures via a low impedance path are completely independent and unrelated to any intended contact or connection to the Earth. The principal purposes for an effectively bonded grounding system via a low impedance path to earth are intended to provide for an applicable reference to earth to stabilize the system voltage of a power distribution system during normal operations and also create a very low impedance path for ground fault current to flow in a “relatively” controlled path. It’s important to carry out earthing tests because of the following reasons:
- A system with faulty grounding can cause catastrophic losses of data, equipment and even human life in case of electrical malfunctions.
- Equipment operating with inadequate grounding may be exposed to voltage surges and spikes that can damage it.
- Sensitive equipment is prone to processing data incorrectly or losing it altogether in case grounding is lost.
- Intermittent faults from bad grounding can create a range of problems, from random shocks to failures that cannot be pinpointed easily.
- A build-up of surface static electricity may give shocks, which are easily misdiagnosed as internal faults. This leads to unnecessary and costly repairs or replacement of parts.
Grounding protects both equipment and human lives, so it is absolutely essential to make sure it’s done right and checked routinely. The world’s best grounding system bonding will be useless unless it can reach a low-impedance ground stake, which makes ground testing all the more essential.
3. Thermography Tests: The temperatures of electrical components and connections are indicative of their health. Excessive heat due to increased electrical resistance will be generated by faulty components and by loose, oxidised or corroded connections. Equipment running hot can also be related to poor assembly, overloading, failure of cooling etc. Thermal imaging is a non-contact on-line technique which can be employed to detect these temperature rises as “hot spots”. Identification of hot spots can be used to trigger remedial work, reducing the number of defects and improving reliability. The two key benefits available from the reduction in defects are:
- Increased plant availability – this can result in very large benefit: cost ratio for key installations supporting business-critical functions, e.g. computer centres. It should also be noted that thermal imaging can be (and is best) done with the plant on-line, reducing the need to take critical plant off-line for testing which in itself would reduce availability.
- Avoidance of consequential damage – this can be damage to the installation itself, connected plant, or other damage due to fire or explosion for example.
4. Arc Flash Risk Assessment & Boundary Determination & Delineation Tests: An Arc Flash is an electrical explosion due to a fault condition or short circuit when either a phase to ground or phase to phase conductor is connected and current flows through the air. Arc flashes cause electrical equipment to explode, resulting in injury or death to workers and destruction of electrical equipment. When an arc flash happens, it does so without warning and is lightning quick. The result of this violent event is usually destruction of the equipment involved, fire, and severe injury or death to any nearby people. Proper safety and protection measures must be taken to limit the damage from an arc flash which include conducting an arc flash study, short circuit study, and NFPA 70E electrical safety training. An Arc Flash Risk Assessment is a calculation performed by a Professional Engineer to determine the thermal incident energy found at each location which determines the various arc flash boundaries and what personal protective equipment (PPE) must be used in approaching each boundary. As part of the study, the engineer shall also provide recommendations to reduce the incident energy / arc flash hazard category.